
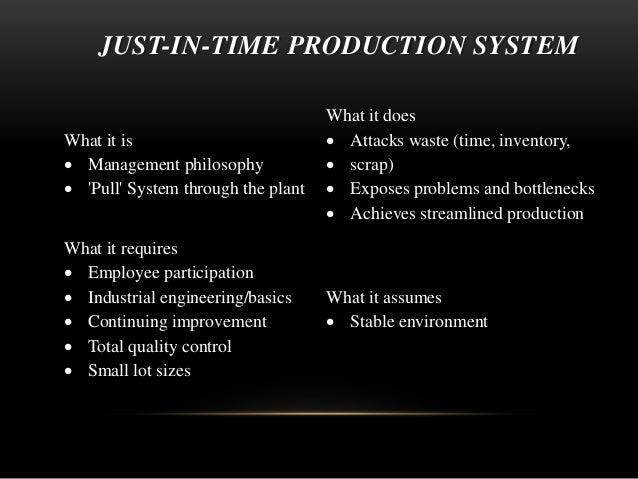
To ensure simplicity and accuracy, the JIT strategy will try to optimize the structure of the product (shown in the Bill of material BOM** diagram) while ensuring quality.Īs a result, the complexity of production planning is reduced, significantly reducing the lead time to the finished product.Įxample Structural diagram of a chair assembly *Shop-floor: production area or workshop (including equipment, warehouses and storage areas, …) where assembly or manufacturing is carried out, either by automated systems or by tools to multiply or combine the two. detailed store inventory reports, end-of-year balance sheets, etc.) will be eliminated or restricted, thereby reducing costs, time, and volume jobs for employees. JIT provides greatly streamlined execution on the shop floor and in purchasing. Where the gray area of the MPC will be most affected by the JIT implementation: Manufacturing Planning and Control (MPC) JIT affects all three areas in MPC including front end, engine and back end. At the same time, control is responsible for ensuring that the process always goes according to plan, or adjusts to changes in the environment.
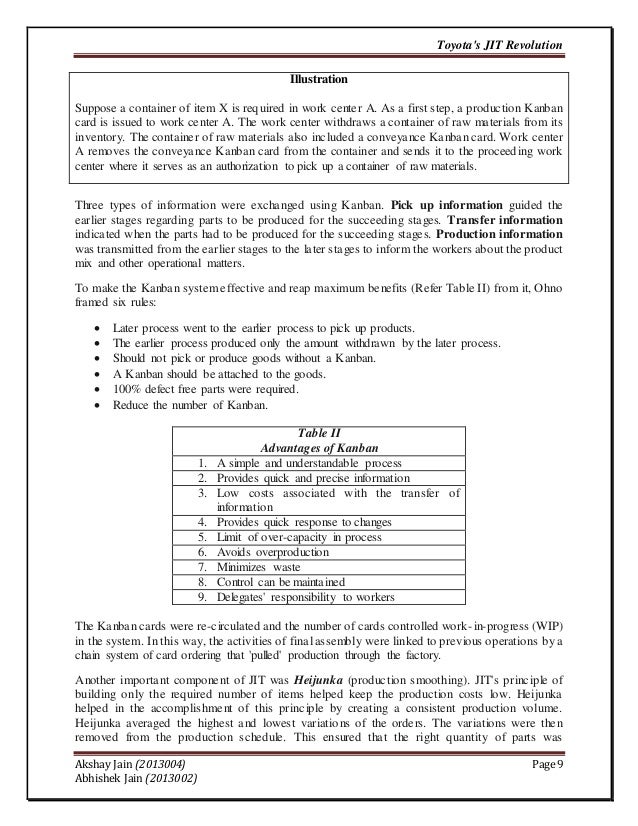
Planning ensures that the goods produced can meet all the needs of the customer. Manufacturing Planning and Control (MPC) is an enterprise’s production planning and control system. How does JIT impact a company’s production planning and control (MPC)? Consequently, this fire cost Toyota 160 billion yen in revenue. This caused a ripple effect, where other Toyota parts suppliers likewise had to temporarily shut down because the automaker had no need for their parts during that time period. Because Aisin is the sole supplier of this part, its weeks-long shutdown caused Toyota to halt production for several days. The prime example is Toyota, which in February 1997, after a fire at Japanese-owned automotive parts supplier Aisin decimated its capacity to produce P-valves for Toyota’s vehicles. If JIT brings tremendous success to Toyota, it also causes this business to suffer. However, JIT is not always a strategy that guarantees the success of businesses that adopt it. Therefore, they always encourage workers to be deeply involved in the product development process. Workers are involved in product improvement: for businesses using JIT, they always think that workers are directly in contact with products, so their feedback is very necessary to improve.Reduce inventory, save warehouse space: with JIT, production will have to be done at the right time, in the right quantity, in the right place, so there is no need for inventory, saving space, and storage costs.Better meet the needs of the market: starting from the feature that all operating processes are simplified, businesses can easily change to better adapt to the needs of customers.Simplified MPC systems: JIT’s goal is to keep things “right”, so businesses tend to simplify all operational processes, making it easier to use this strategy as much as possible.Reduce the number and cost of transactions: when applying the JIT strategy, businesses almost have to maintain everything right and just right, thereby minimizing the amount of returned goods, and always keeping the inventory warehouse to a minimum, thereby reducing costs such as transportation costs, warehousing costs, bookkeeping costs, etc.Reduced production time (the amount of time it takes for a product to be converted from raw materials to finished products) as JIT has minimized waiting times between stages in the process.Inside Toyota’s factory The benefits of using the Just-in-time (JIT) įact: JIT was first applied by Toyota in 1970 and it is considered the key to their success. JIT is implemented to ensure the production of “the right product, in the right quantity, in the right place, at the right time” with the goal of “no inventory, no waiting time, no additional costs”. Just-in-time (JIT) is an inventory management strategy whose primary goal is to adjust the flow of materials in line with production schedules and customer orders. The success of JIT is ensured by four basic elements: product design, process design, human/organizational factors, production planning and control.JIT affects all three areas of the production planning and control system, including the front end, engine, and back end.Just-in-time (JIT) is an inventory management strategy that aims at “ no inventory, no waiting time, no additional costs ” during operation and production.So what is the secret to Toyota’s success? That is the lean production system model and Just-in-time is the key. TOPLINE Toyota is Japan’s leading automobile manufacturer, with a history of nearly 100 years, Toyota is continuing to assert its position in terms of quality, price and ability to meet customers’ needs.
